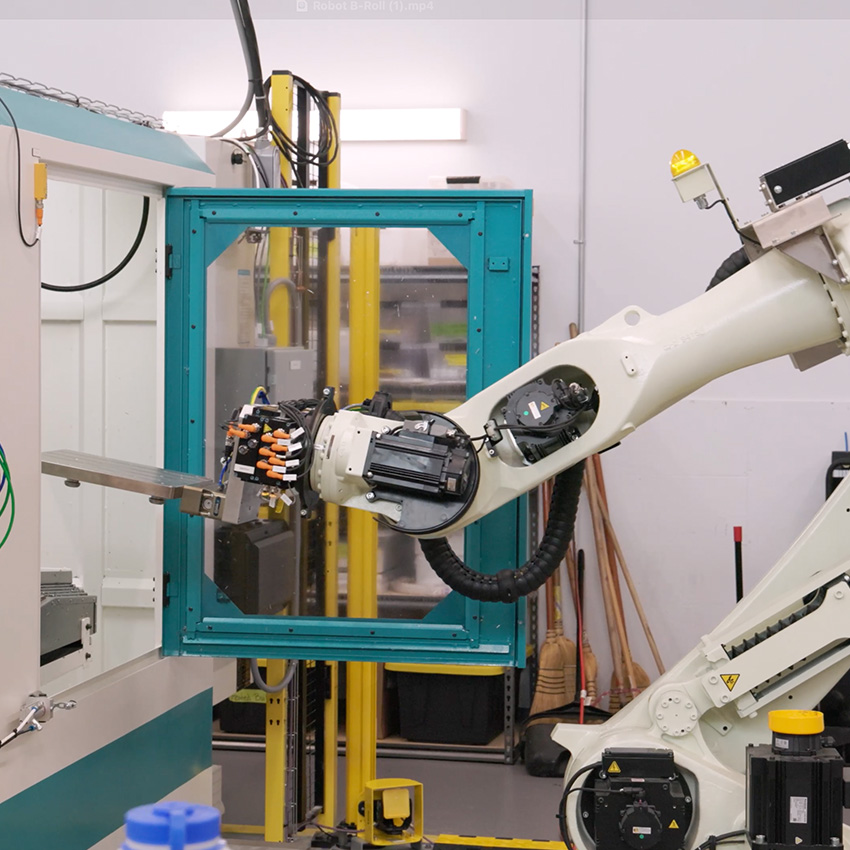
Smart Manufacturing and Automation
Smart manufacturing and automation leverage advanced technologies for real-time data collection, analysis, and decision-making, resulting in more efficient, adaptable, and responsive production systems. These innovations are essential for maintaining a competitive edge globally, enabling industries to cut costs, enhance product quality, and accelerate production.
Digital and Intelligent Manufacturing
Artificial Intelligence in Manufacturing
Artificial Intelligence (AI) is transforming manufacturing by enhancing efficiency, precision, and innovation. At GTMI, our work in AI for manufacturing is exemplified by the Georgia AIM (Artificial Intelligence in Manufacturing) initiative. This project aims to position Georgia as a leader in AI manufacturing by integrating AI technologies across various sectors and communities. Through partnerships with industry, government, and educational institutions, Georgia AIM focuses on developing AI-driven solutions that improve production processes, reduce costs, and create high-paying jobs.
Our research includes the application of machine learning for predictive maintenance, optimization of manufacturing workflows, and the development of intelligent systems for real-time process monitoring and control.
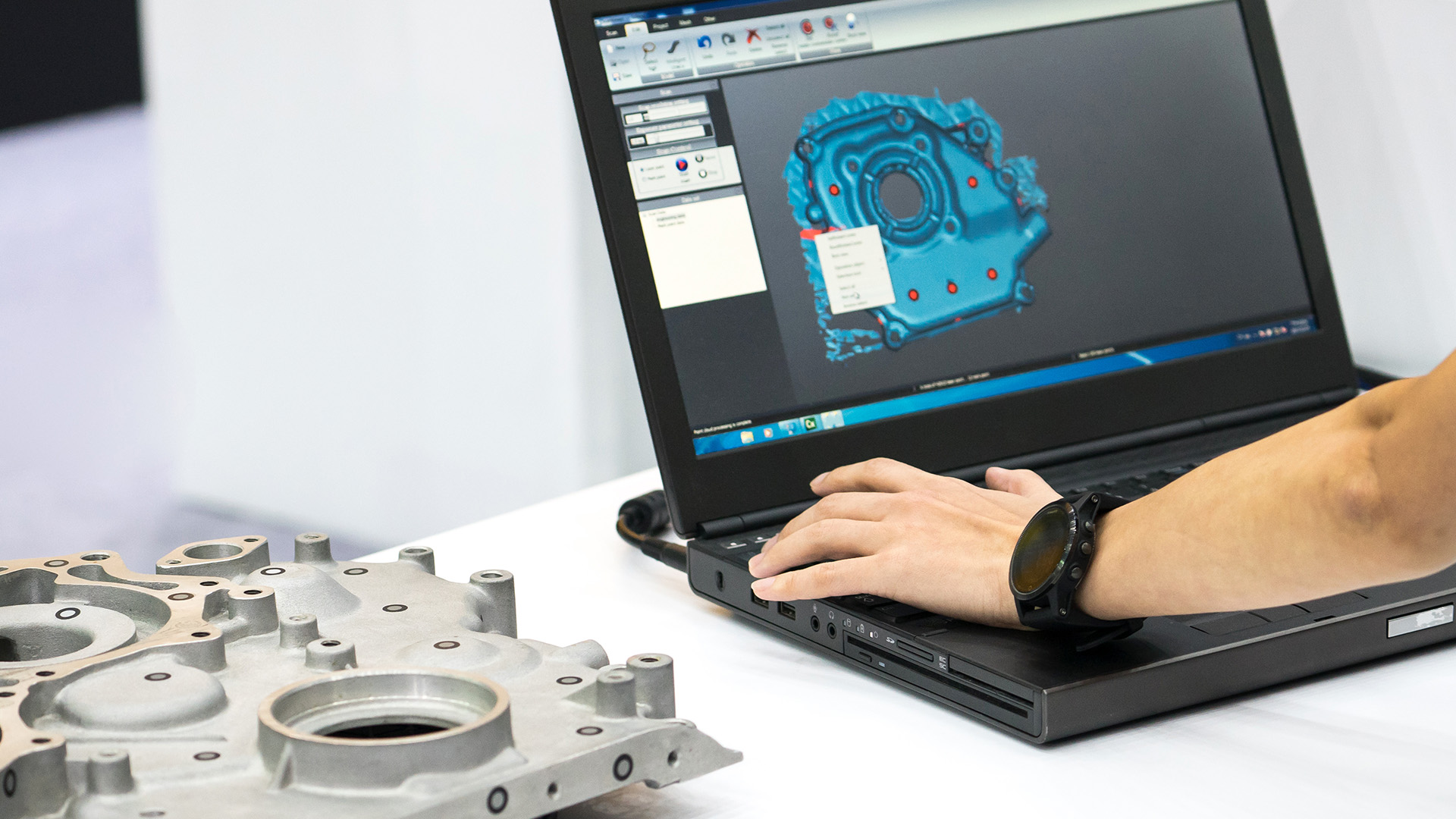
Digital Manufacturing
Digital manufacturing leverages advanced digital technologies to enhance and streamline manufacturing processes. This includes the use of IoT, machine learning, cloud computing, and data analytics to create more efficient, flexible, and responsive production systems. At the Georgia Tech Manufacturing Institute (GTMI), our work in digital manufacturing drives innovation and industry collaboration. We develop cutting-edge technologies to improve efficiency, reduce costs, and increase productivity across various sectors. Our initiatives include secure supply chain design, optimized product development, and predictive maintenance.
Internet of Things for Manufacturing and Factory Information Systems
The Internet of Things for Manufacturing (IoTfM) is transforming the factory floor, and GTMI’s Factory Information Systems Center (FIS) is at the forefront of this revolution. With 25 years of experience, GTMI helps companies increase predictability, reduce costs, and improve productivity through technological roadmap development, custom projects, and consortia collaborations. Our expertise includes factory architectures, machine communication, cloud computing, edge devices, machine learning, predictive maintenance, overall equipment effectiveness (OEE), and cybersecurity. GTMI also hosts an annual IoTfM symposium and a Manufacturers’ Roundtable to foster industry collaboration and innovation.
Automation Technologies
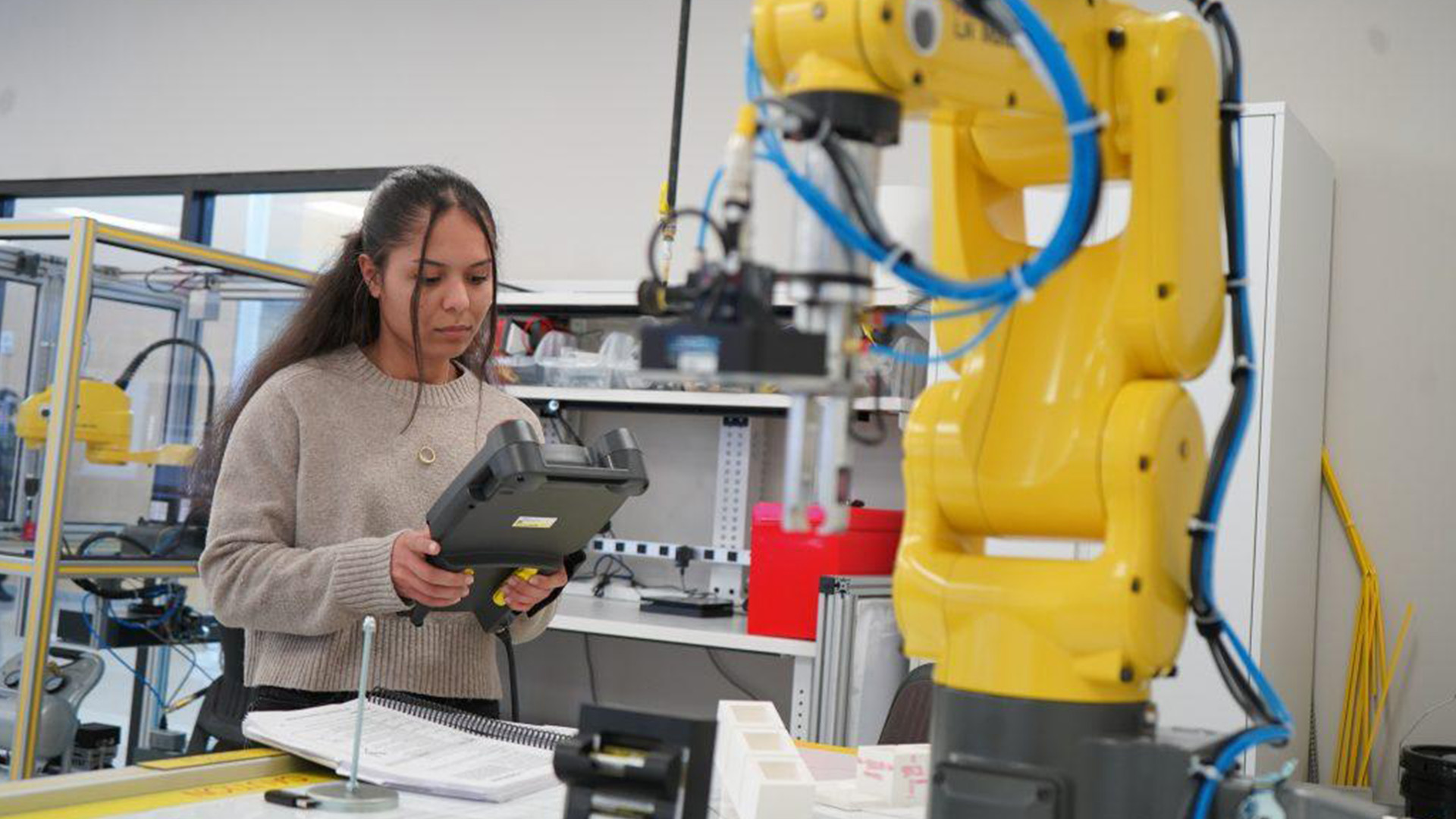
Flexible Automation
Advanced manufacturing and assembly require flexible automation technologies to enhance production efficiency and product quality, especially for high product mix and variable volumes. While industrial robots offer flexibility, they lack the precision needed for certain tasks. GTMI and the Institute for Robotics and Intelligent Machines (IRIM) are developing flexible automation technologies for precision manufacturing. Research focuses on accurate industrial robotics, data-driven modeling of robot behavior, hybrid manufacturing systems, and robotics for biomanufacturing. Supported by industry and government, this work includes close collaboration with industry at the Boeing Manufacturing Development Center and is backed by IRIM and the Advanced Robotics for Manufacturing (ARM) Manufacturing Innovation Institute.
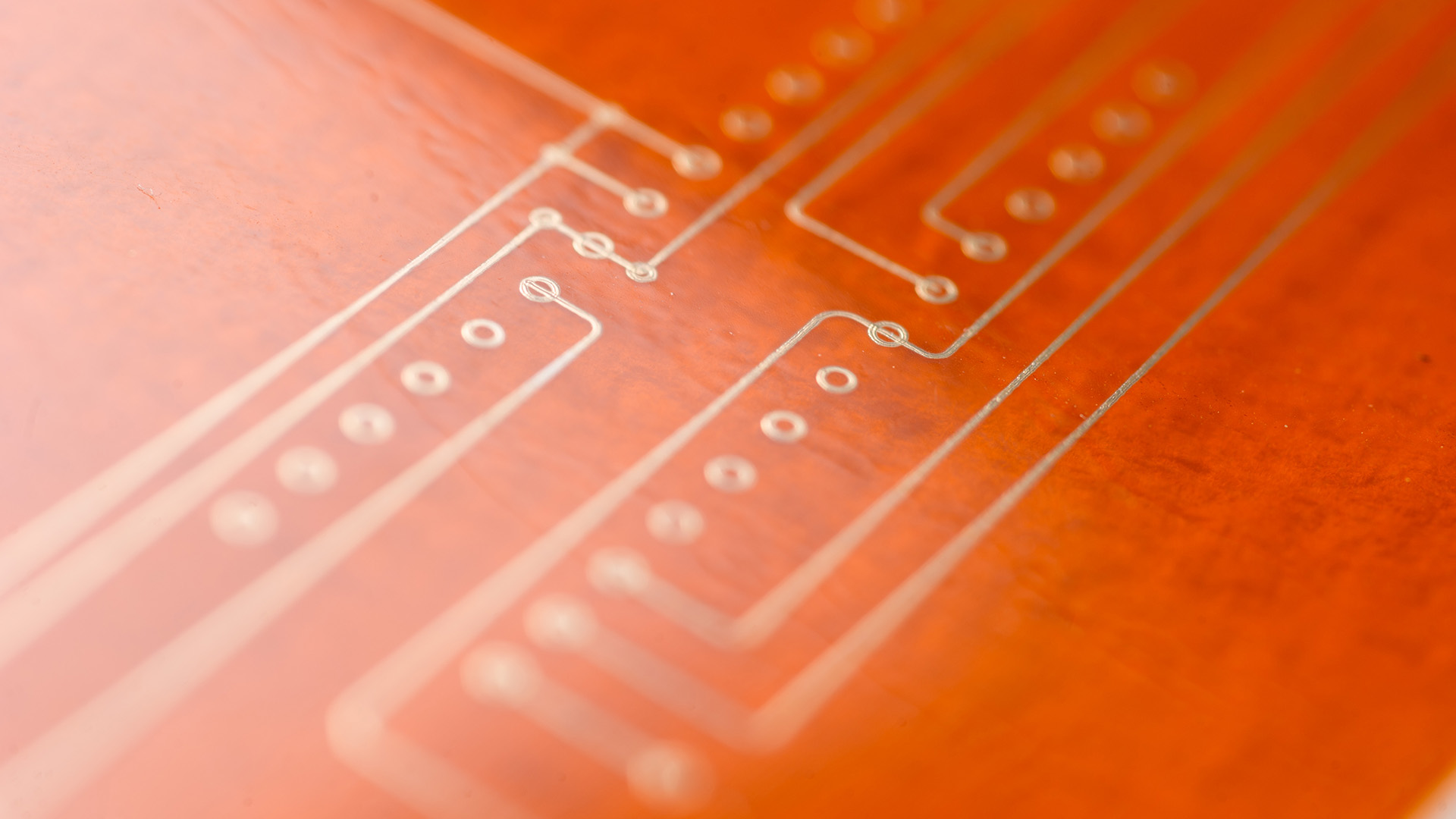
Automation Pathways
Automation pathways refer to the systematic application of interconnected technologies that optimize entire manufacturing processes, rather than just automating individual tasks. Unlike traditional automation, which often focused on isolated systems or specific machines performing set functions, automation pathways create a network of technologies—such as IIoT, AI, and machine learning—that work together across the entire manufacturing operation. This interconnected approach enables systems to communicate and adapt in real time, allowing for continuous optimization, predictive maintenance, and quicker responses to production changes. In contrast to older methods that relied on predefined, static workflows, automation pathways offer more flexibility and the ability to dynamically adjust to evolving needs, making operations more resilient and efficient over time.
GTMI implements automation pathways by addressing the entire manufacturing architecture, ensuring that the necessary technologies to drive improvements throughout an organization can be integrated in a cost-effective and technically feasible manner. This holistic approach enables a wide variety of technological solutions to be applied to both specific and broad challenges.
Human-Centric and High-Throughput Systems
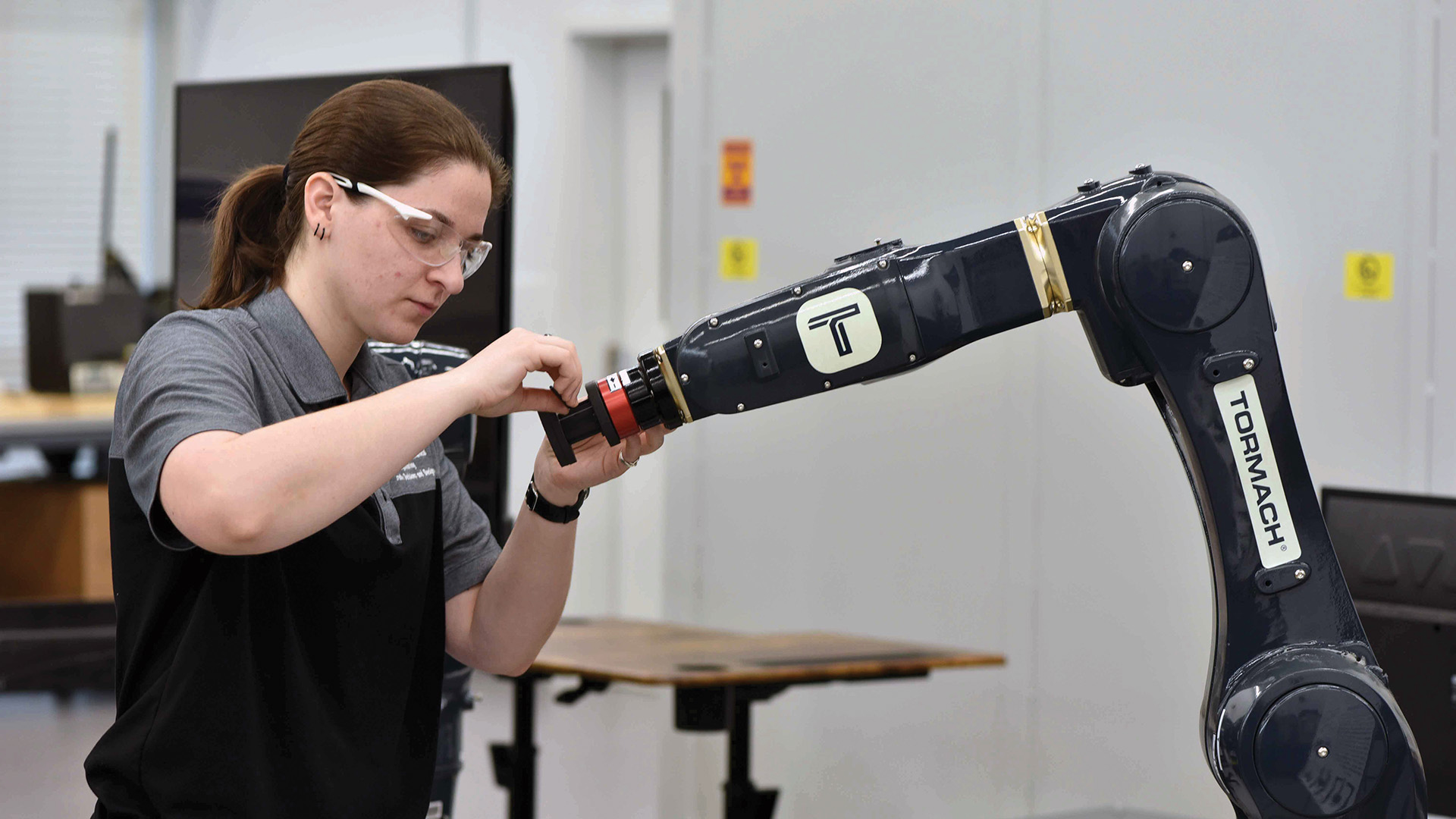
Human-Centric Design
Human-centered design employs design principles, frameworks, and computational tools to develop innovative products and manufacturing systems. At its core, human-centric design in manufacturing prioritizes human needs and societal challenges. By understanding the capabilities and limitations of both people and existing technologies, and designing systems that support people's well-being and productivity, we can create more efficient, effective, and sustainable manufacturing operations.
GTMI is advancing human-centric design by utilizing cutting-edge design methods to develop new manufacturing processes and the products they enable, enhance product quality by minimizing defects and focusing on user needs, and increase efficiency and sustainability by reducing waste and streamlining workflows.
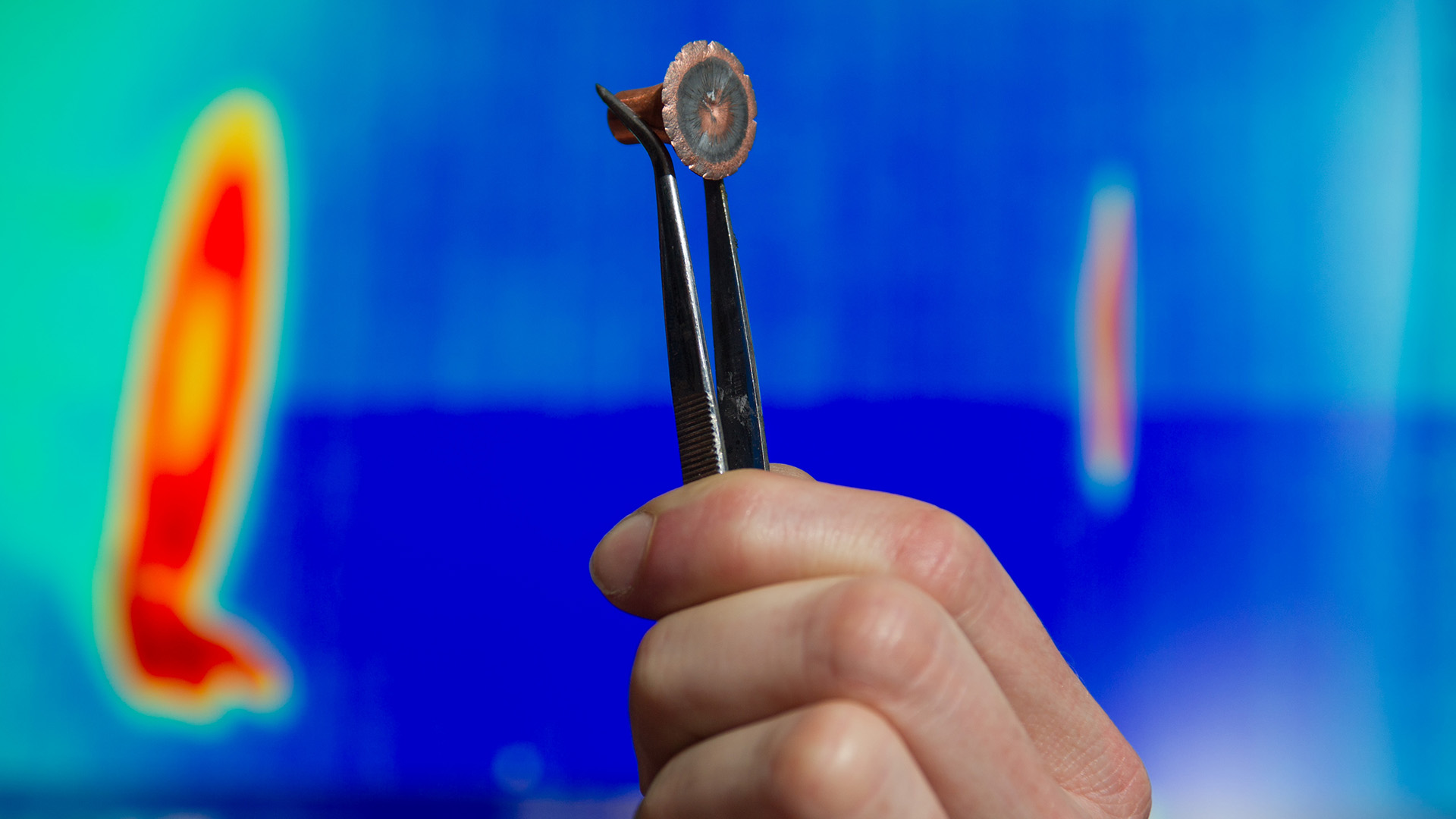
High-Throughput Characterization
High-throughput characterization accelerates innovation and boosts manufacturing efficiency by rapidly analyzing materials and processes. Unlike traditional methods that are slower and more limited in scope, it employs advanced tools such as automated microscopy, spectroscopy, and data analytics to evaluate multiple parameters across large sample sets. This enables swift identification of material properties, defects, and performance metrics, supporting faster decision-making and optimization.
At GTMI, high-throughput characterization is seamlessly integrated into the manufacturing workflow through cutting-edge technologies. This allows for real-time data collection and quality assurance, ensuring materials and processes meet rigorous standards. By embracing these methods, GTMI enhances agility, drives continuous improvement, and remains responsive to evolving industry needs.