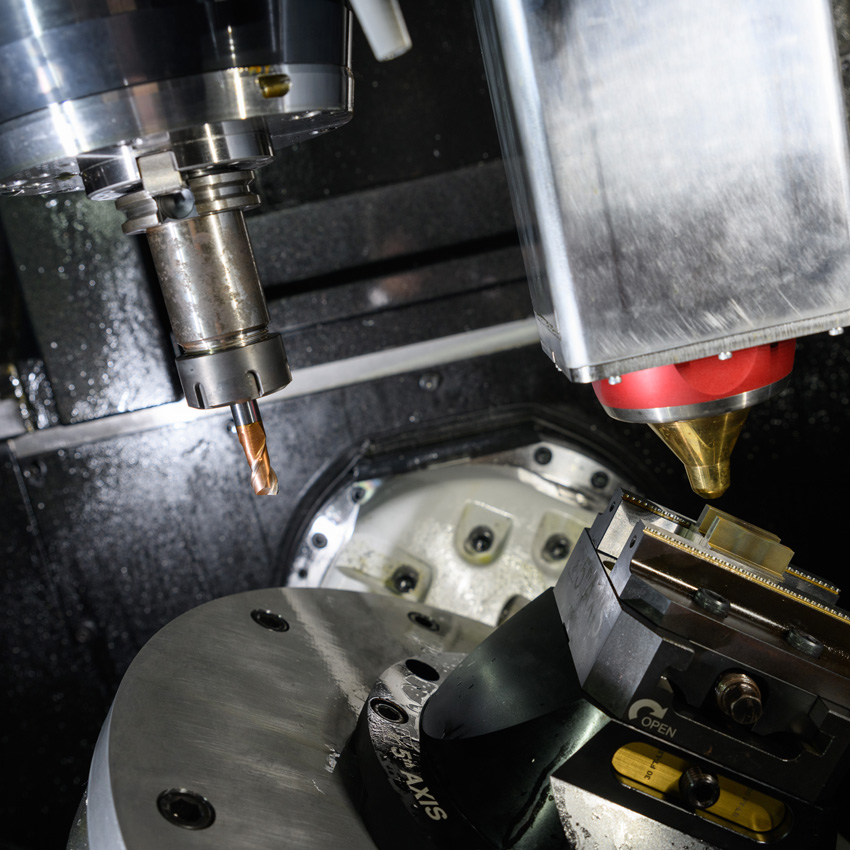
Manufacturing
GTMI’s manufacturing capabilities span the full spectrum of modern production — from advanced additive and hybrid techniques to precision machining and sustainable material processing. Our state-of-the-art facilities support the development of complex components, rapid prototyping, and scalable solutions for a wide range of materials.
Additive and Hybrid

Additive and hybrid manufacturing involve creating parts by adding material layer by layer, often using advanced 3D printing technologies. These methods are essential for rapid prototyping, producing complex geometries, and enabling customized production. At GTMI, our advanced capabilities in metals and polymers drive innovation and efficiency in modern manufacturing processes.
Metals
GTMI’s metals capabilities span the full spectrum of manufacturing — from traditional machining to cutting-edge additive and hybrid processes. Our focus on material performance, structural integrity, and process optimization ensures that metal-based innovations meet the highest standards of quality and functionality.
Electron Beam Powder Bed Fusion (EB-PBF)
This process uses a high-energy electron beam to selectively melt metal powders, layer by layer, to create intricate components. Featured tool: FreemeltONE.
Laser (L-PBF)
This method employs a laser to melt metal powder particles onto a build plate, layer by layer, enabling the creation of complex metal parts. Featured tool: Aconity MIDI+.
Directed Energy Deposition (DED)
DED forms 3D objects by melting material as it is deposited using focused thermal energy, such as a laser or electron beam. Featured Tool: Optomec DED Hybrid.
Hybrid – 5-Axis Additive/Subtractive
This process combines additive manufacturing with traditional subtractive machining, allowing for the creation and refinement of parts in a single setup. Featured tool: Mazak VC-500AM Hybrid.
Wire arc Additive Manufacturing (WAAM)
WAAM uses an electric arc as a fusion source to melt wire feedstock, building up parts layer by layer. Featured tool: Coming soon.
Polymers
GTMI’s polymer capabilities support the development of high-performance materials and components through both additive and traditional manufacturing methods. Our research and facilities enable rapid prototyping, customization, and scalable production, driving innovation in sustainable and functional polymer applications.
Fused Deposition Modeling (FDM)
FDM involves depositing melted plastic filament layer by layer to build up a 3D object. It is widely used for prototyping and producing durable parts. Featured tool: Coming soon.
Powder Bed Fusion
This additive manufacturing process uses a high-energy source, such as a laser or electron beam, to selectively melt and fuse powdered material layer by layer. It is ideal for creating complex, high-precision components. Featured tool: Coming soon.
Photopolymer Resin Printers
These printers use UV light to cure liquid resin layer by layer, producing highly detailed and precise parts. Featured tool: Formlabs 3+ Resin Printer.
Machining
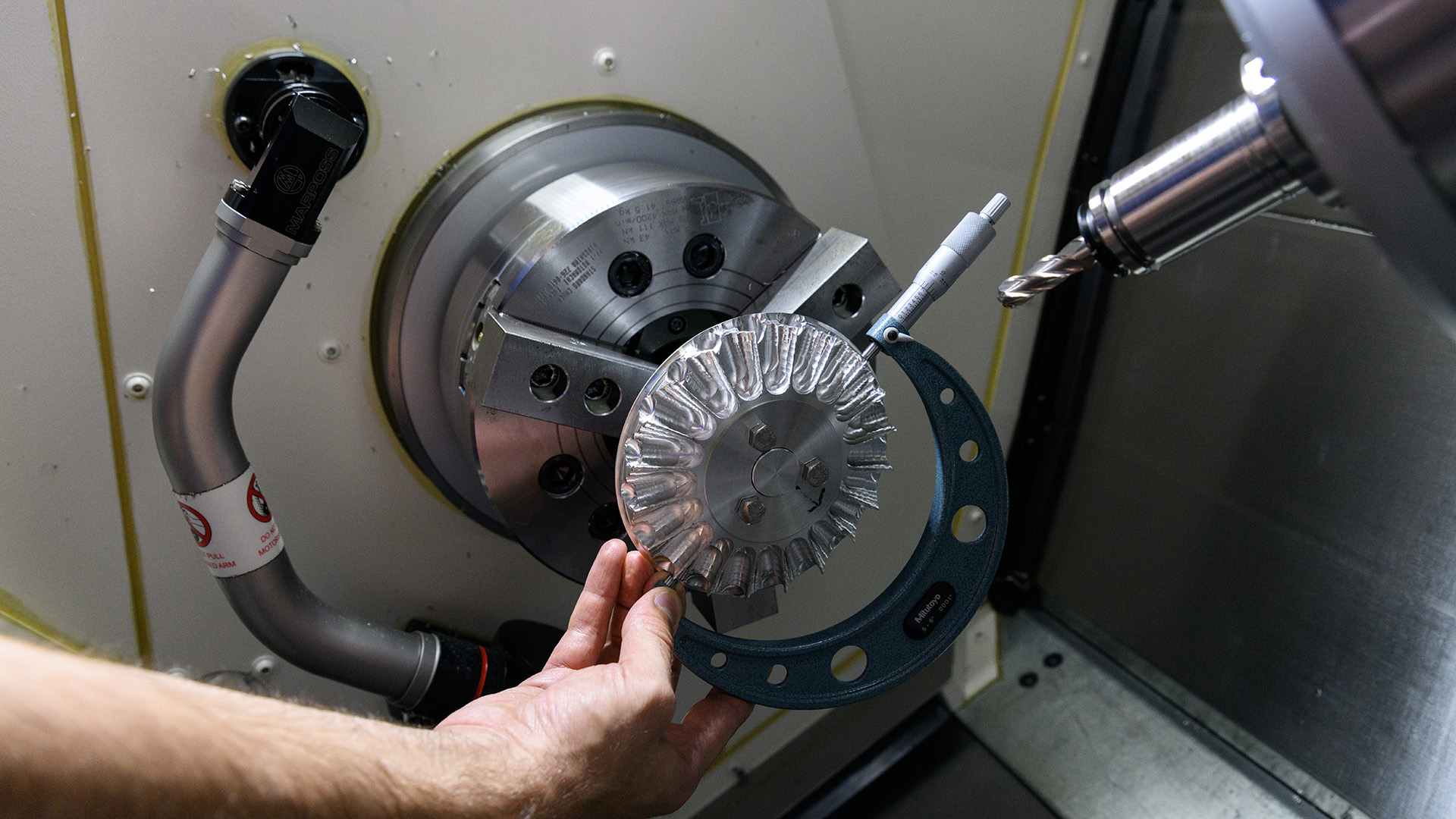
Machining involves the precise removal of material to shape parts and components, using advanced techniques and general fabrication tools. These methods are crucial for producing high-precision parts, enabling complex geometries, and ensuring consistent quality. GTMI's advanced machining capabilities enhance product quality and accelerate the manufacturing process, ensuring high standards and fostering technological advancements.
5-Axis Wire EDM
This process uses electrical discharges to cut complex shapes with high precision, allowing for intricate and detailed parts. Featured tool: Makino U6 Wire EDM.
Multiple-Axis CNC Milling
This technique involves using computer-controlled rotary cutters to remove material from a workpiece, enabling the creation of complex geometries with high accuracy. Featured tool: Mazak VCU CNC Mill.
CNC Turning
CNC turning uses computer-controlled lathes to rotate the workpiece while cutting tools shape it, ideal for producing symmetrical parts. Featured tool: Coming soon.
General Fabrication Tools
These tools encompass a variety of equipment used for cutting, shaping, and assembling materials, essential for general and often manufacturing tasks.
anchor
Synthesis and Recycling
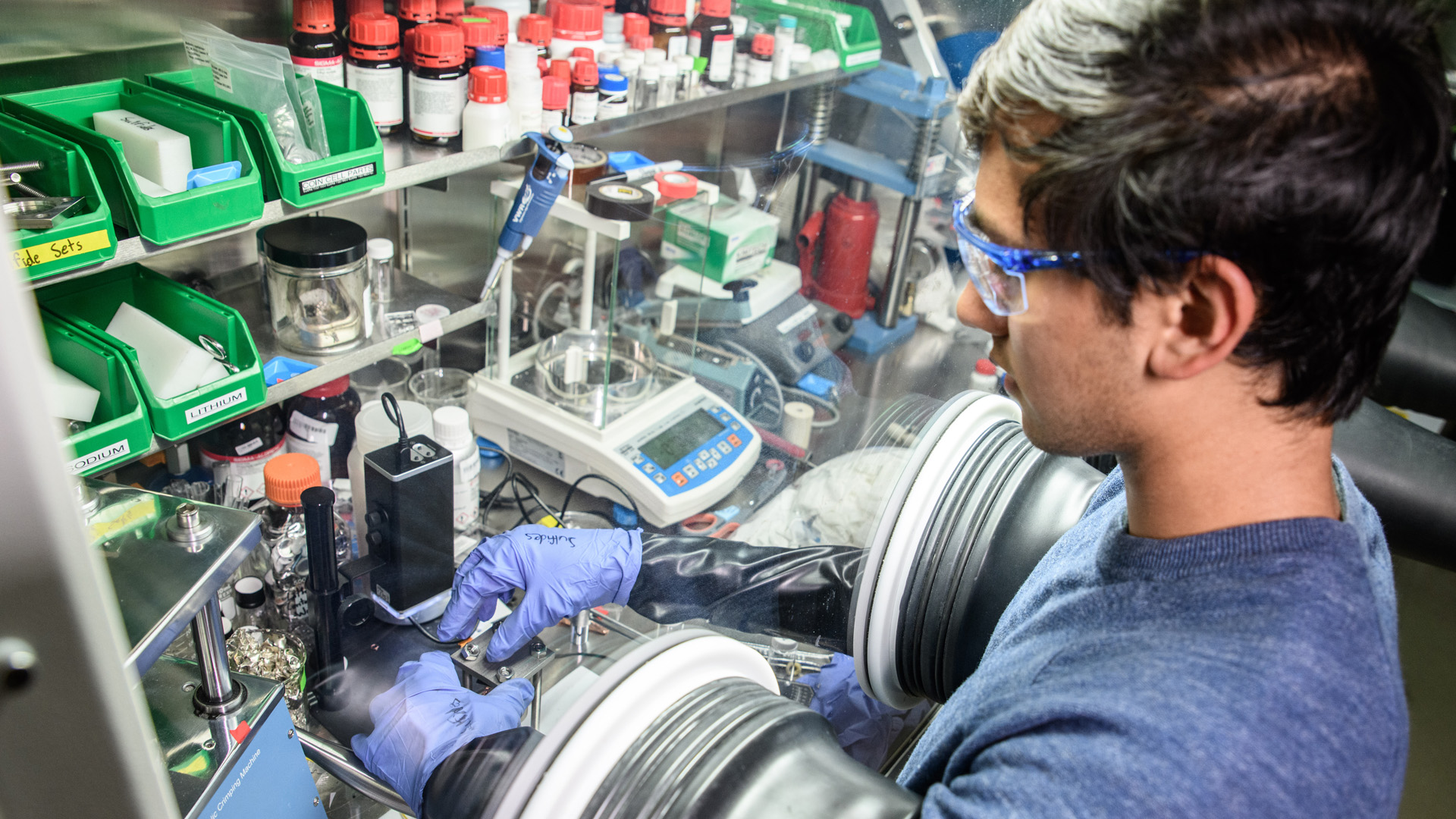
Synthesis and recycling involve metal alloying, the creation of new materials, and the repurposing of existing ones to enhance sustainability and innovation in manufacturing. These processes are essential for developing advanced materials, reducing waste, and promoting eco-friendly practices. At GTMI, our cutting-edge synthesis and recycling capabilities drive impactful advancements in modern manufacturing, ensuring a sustainable future.
Powder Atomization
This process involves converting molten metal into fine powder particles, which are then used for various manufacturing, alloy development, and recycling applications. Featured tool: Amazemet rePOWDER.
Wire Drawing and Sheet Rolling
Wire drawing reduces the diameter of metal wire by pulling it through a die, while sheet rolling involves passing metal sheets through rollers to achieve desired thickness. Featured tools: Rolling Mill Suite.
Powder Processing
This involves handling and treating metal powders to prepare them for manufacturing, ensuring optimal properties and performance.
Casting
Casting involves pouring molten metal into a mold to create parts with specific shapes and properties.
Heat Treating
This process uses controlled heating and cooling to alter the physical and mechanical properties of materials, enhancing their performance.
Sheet and Rod Forming
This involves shaping metal sheets and rods into desired forms using various techniques.